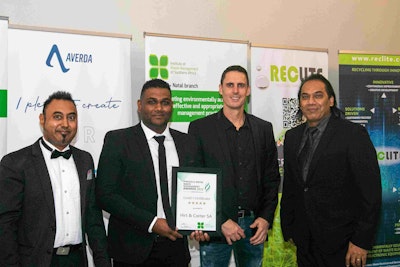
Three Averda clients win at the 2022 IWMSA KwaZulu-Natal Branch Waste Management Awards
Averda is delighted to announce that three of our clients – Defy Appliances, Toyota South Africa Manufacturing, and Hirt & Carter South Africa – were recognised for their achievements practising effective waste management and sustainability initiatives in the KwaZulu-Natal province.